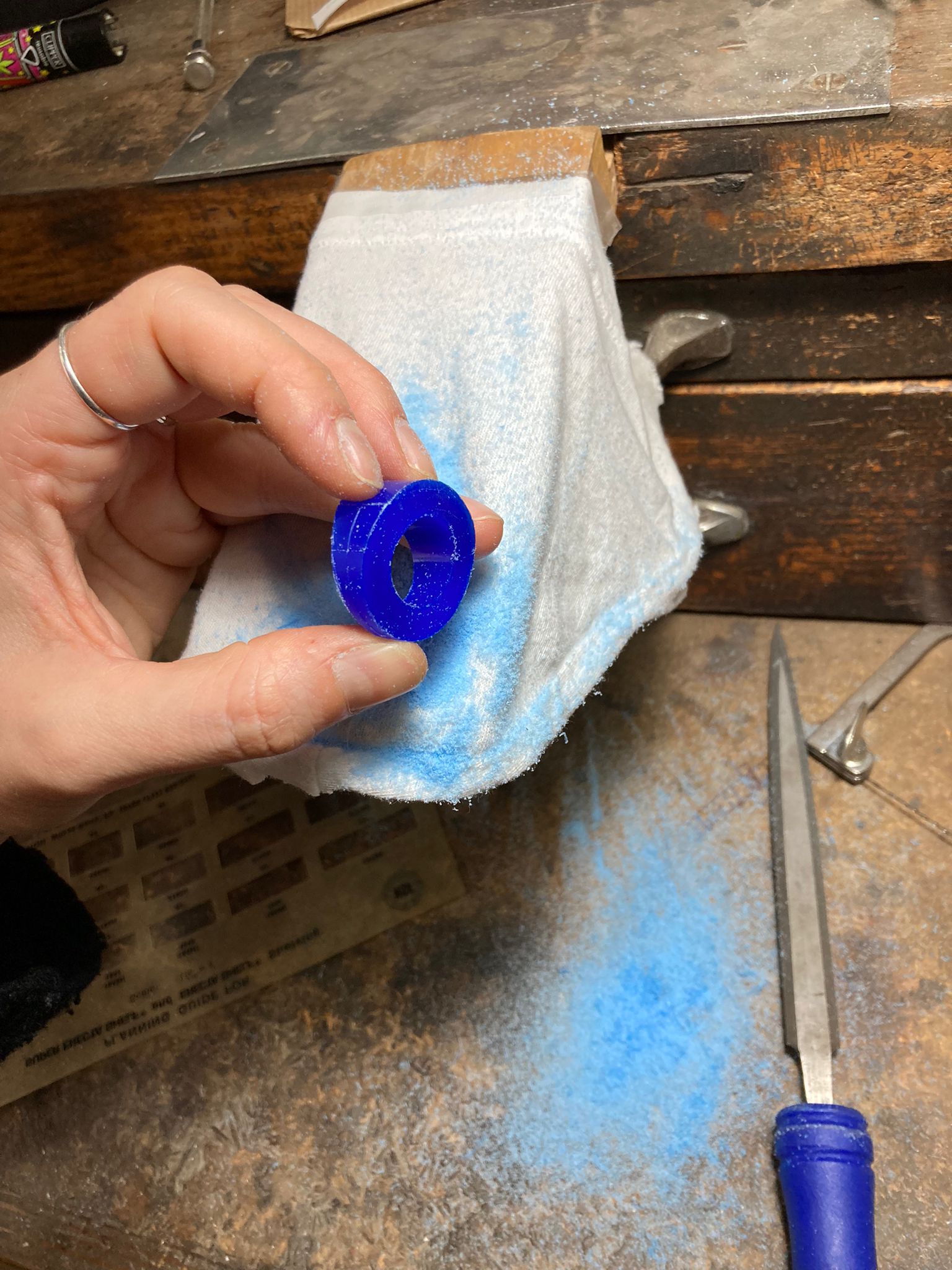
THE WORKSHOP
Artisan handmade jewels to empower
How do we do it?
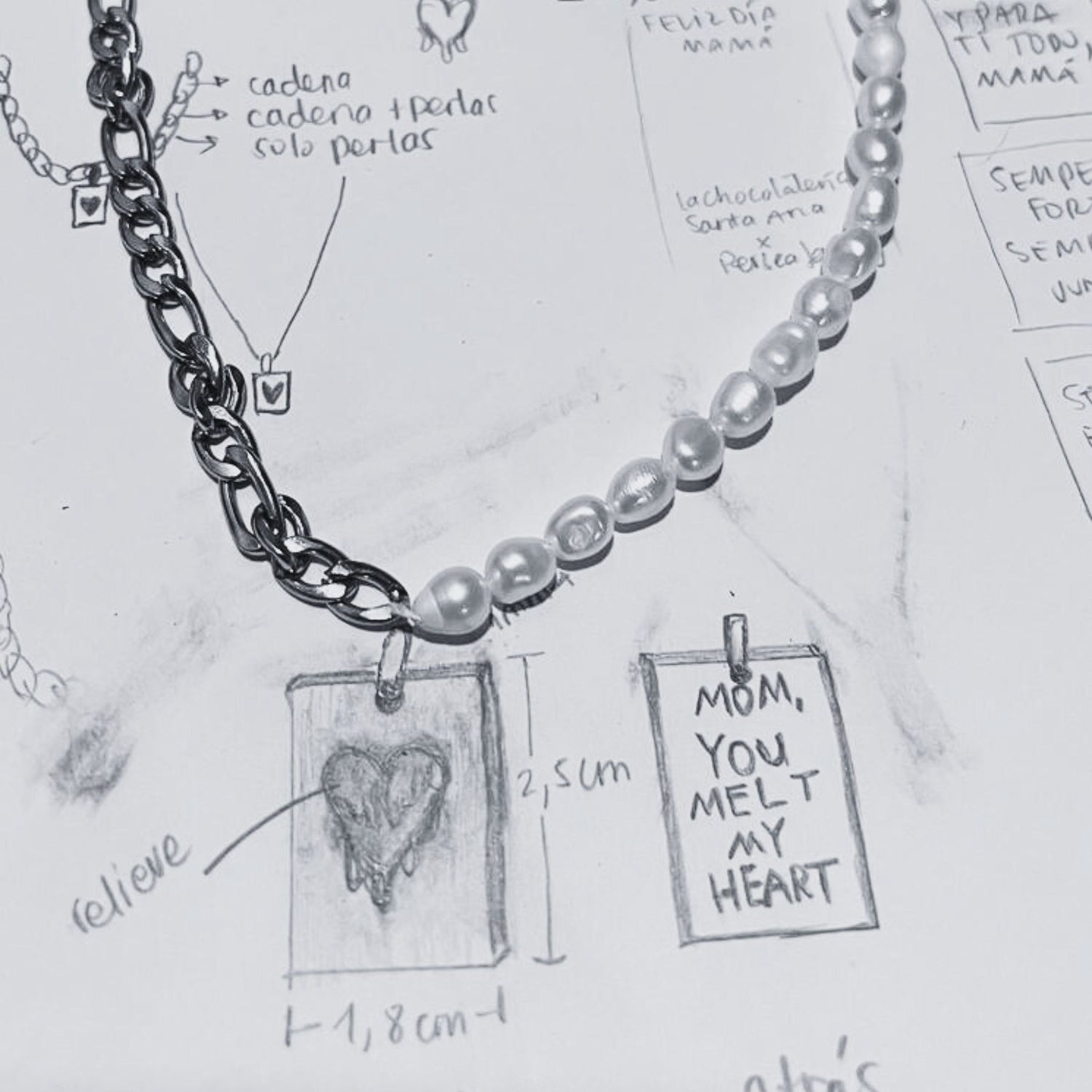
Creation
Floating creativity and design on paper
Each design is our own and unique. After having a theme in mind and having been inspired, we take paper and pencil and let ourselves flow.
No limits, no judgement. We draw and manage collections that have a purpose, that tell stories and that connect.
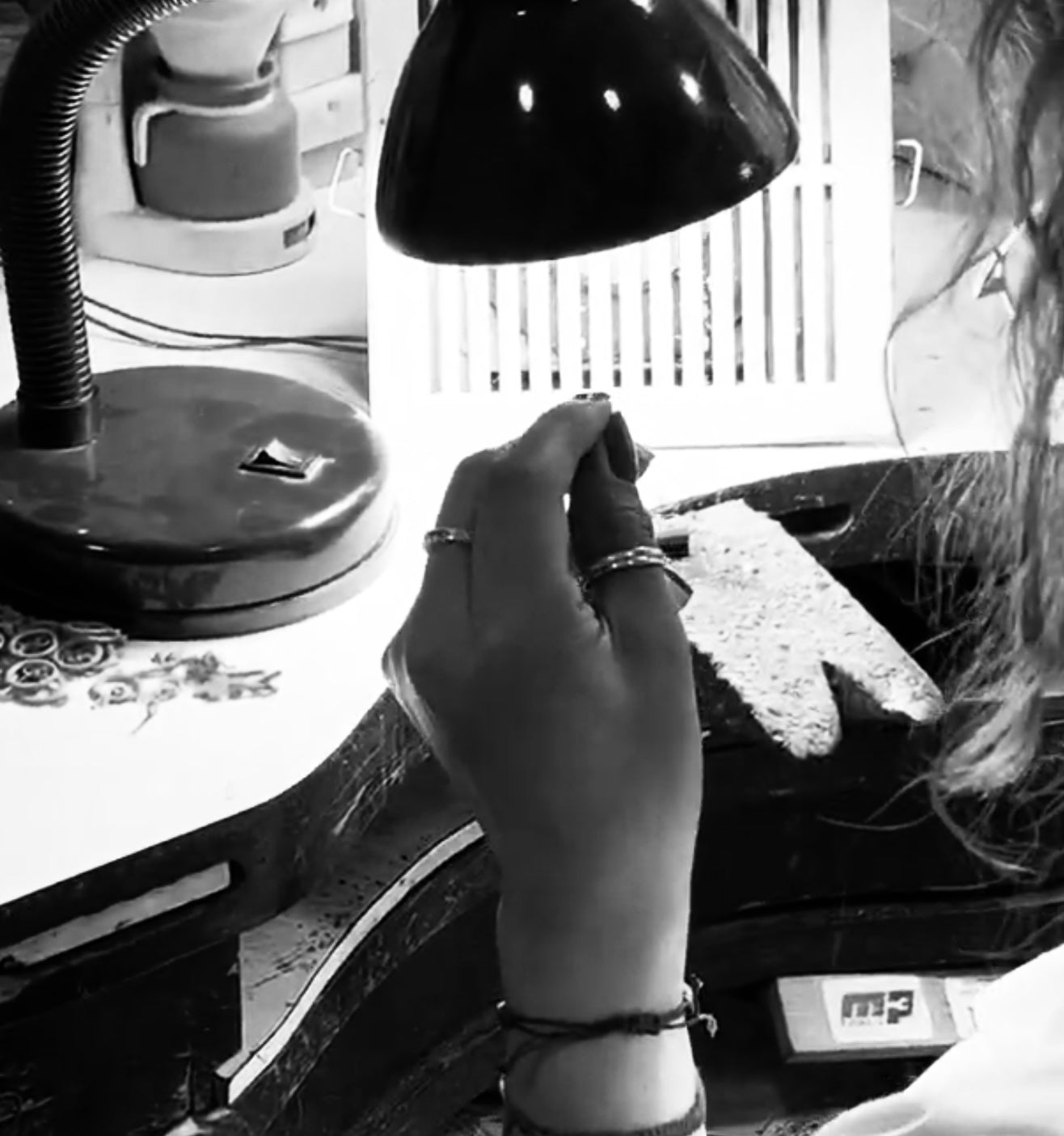
Projection
We land the designs on something material
Pair text with an image to focus on your chosen product, collection, or blog post. Add details on availability, style, or even provide a review.
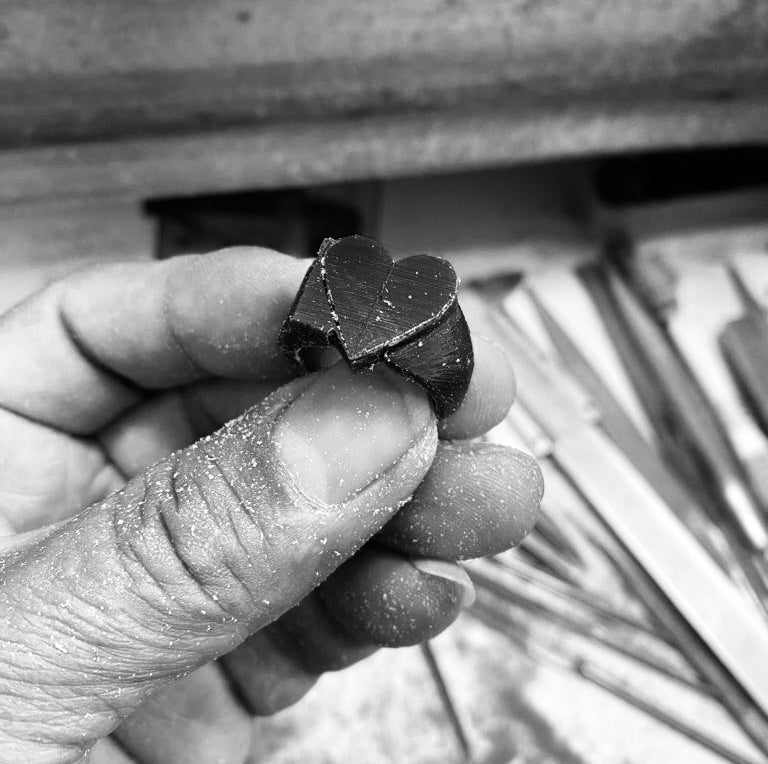
Modeling
Wax Molds
Following the Lost Wax Casting technique, artisans like Dani and Orfa will carve all the designs by hand in wax. It is one of the oldest jewelry techniques.
This way we ensure that the designs are 100% organic and unique and that we also employ people and not machines.
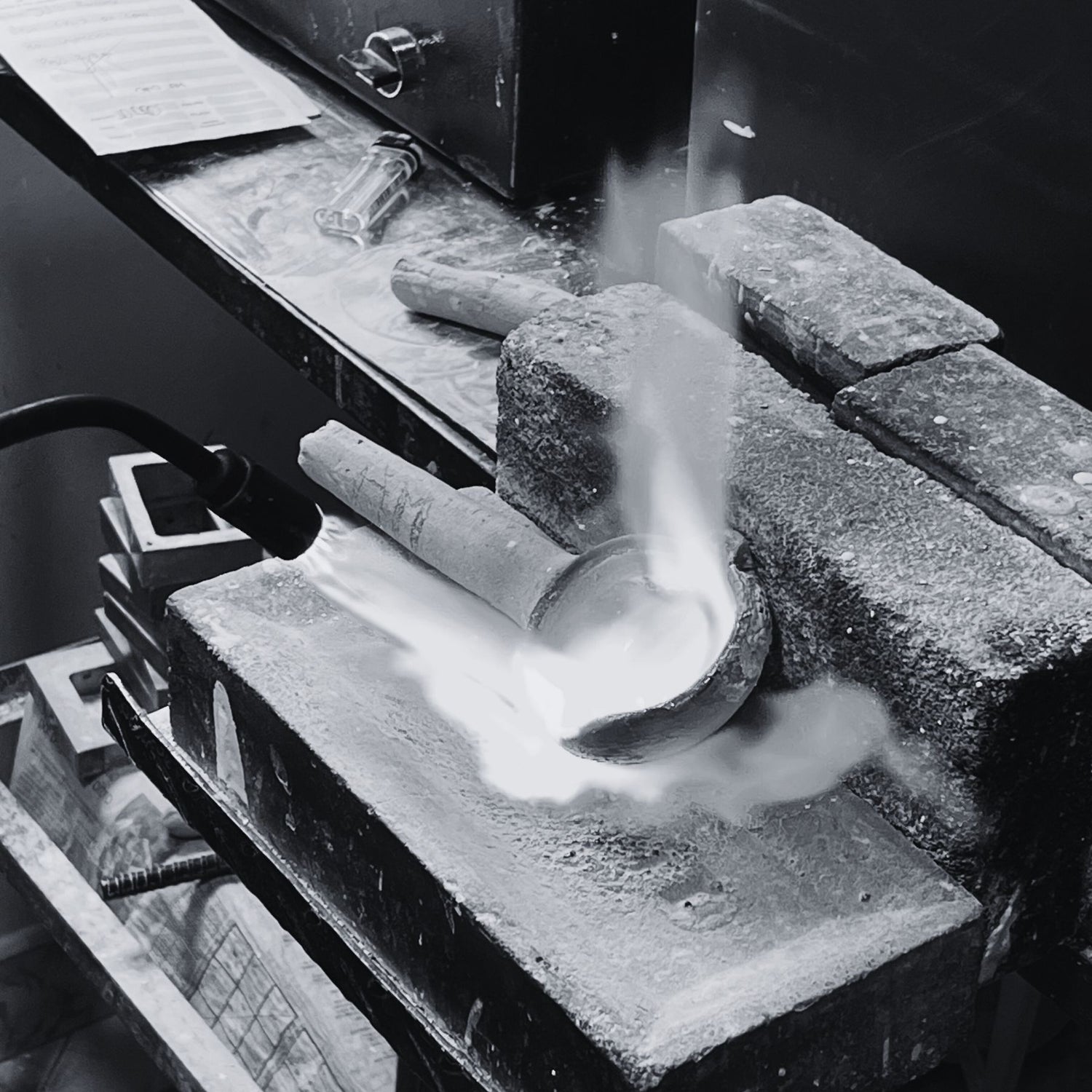
Foundry
Metal casting
After several versions, we approved the final prototype which is exactly (or better) what we had in mind. Using the Casting technique, the wax is melted and a rubber mould is created.
This will be the basis for creating several units of the same design, creating several copies of that mold and melting the metal (silver or bronze) to make the jewelry.
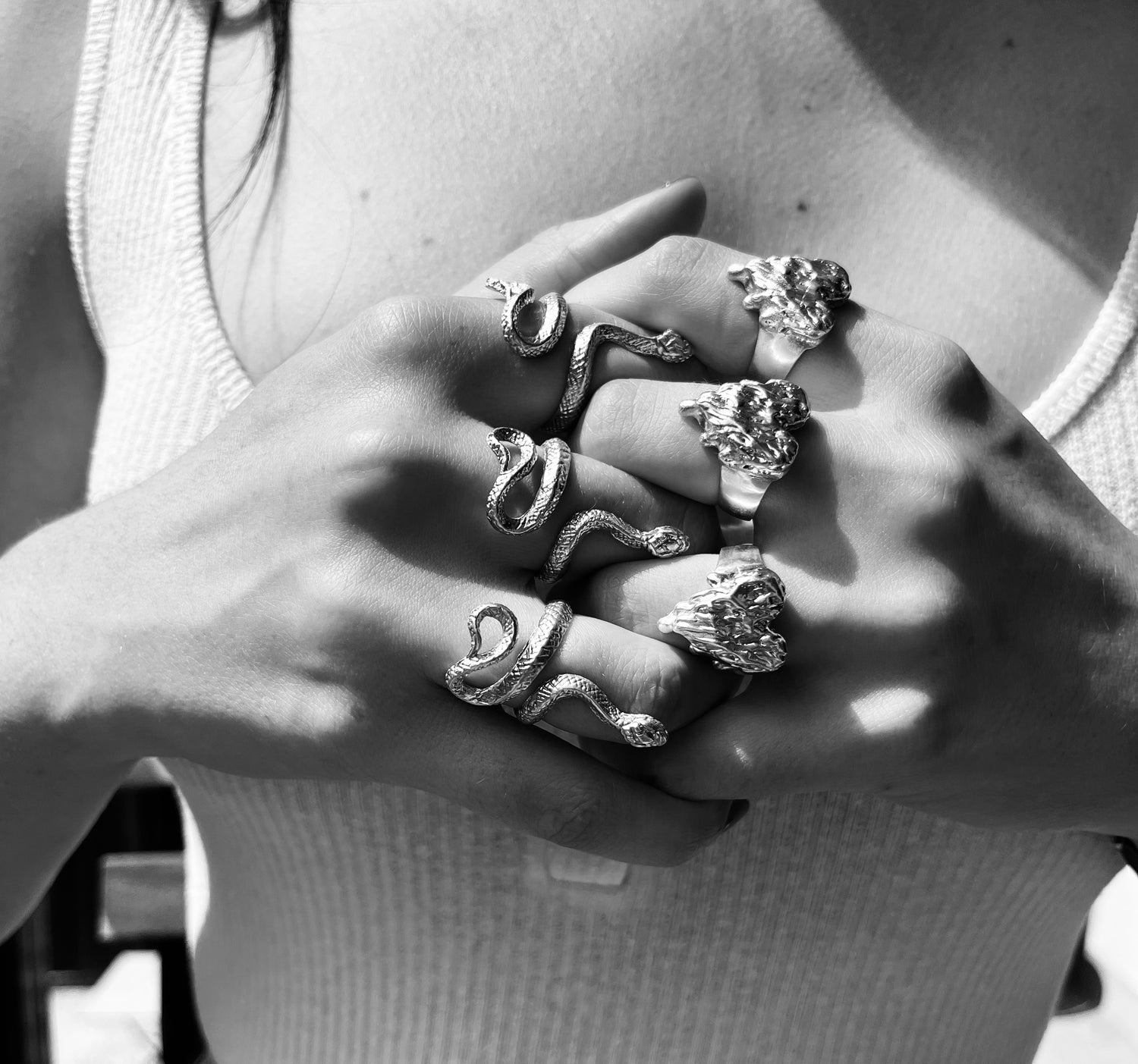
Ending
Final finishes and veneer
The jewels are then washed, polished, and repaired so that the bronze ones can be plated with gold.
We make sure it is a 6 micron 21kt gold plating to ensure the color lasts longer.

Conclusion
Quality control and final lacquering
Although this is done at each stage, at the end we go back and examine each piece of each production one by one to ensure that they are all in perfect condition.
Those that pass the filter, normally 90%, will undergo a final phase of cataphoretic lacquering to further brighten and prevent the deterioration of the jewel in every possible way.
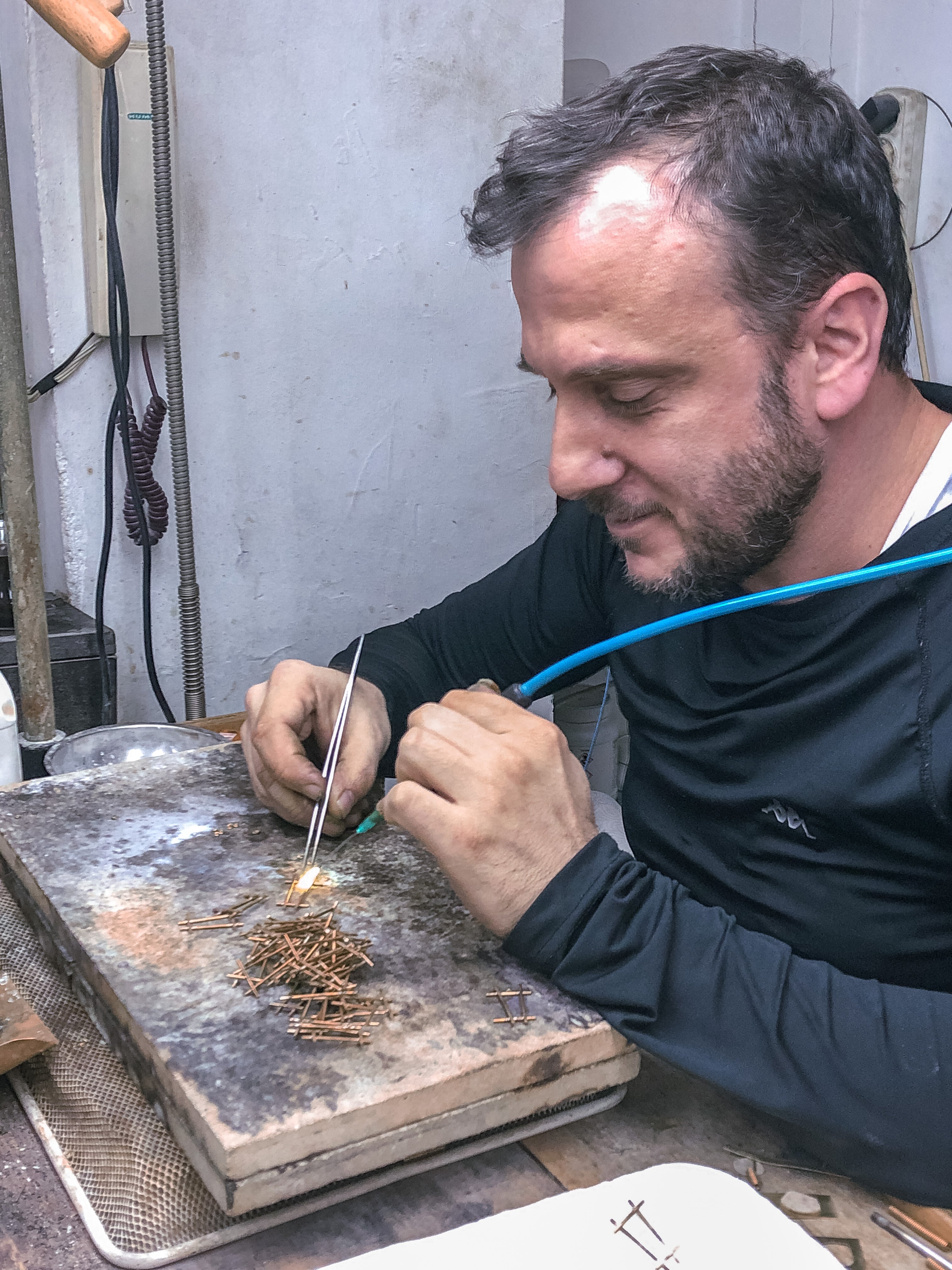
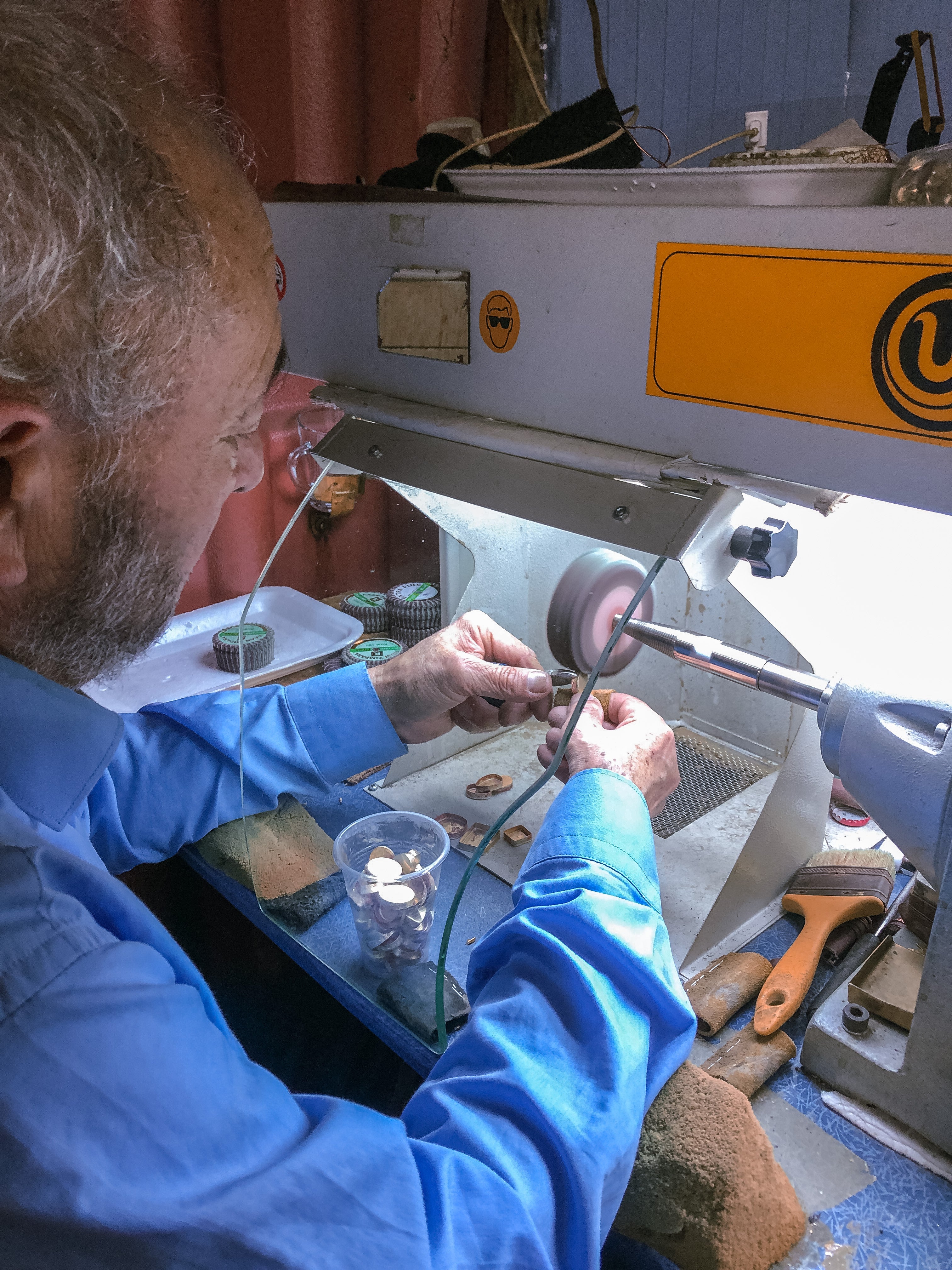
